As LED technology advances, various types of LED chips emerge. No one would want to know nothing but the brand of the chips while choosing, so here is a simple guide to let you learn about some basic classifications of the chips, which include packaging technology, power, and color. Understanding these differences is crucial when selecting the most suitable LED chips for your specific needs. You will find choosing LED chips not difficult anymore with the information in the following passage!
Different LED packaging types
DIP
DIP is a traditional way to package electronic components, and the full name is “Dual In-Line Package.” The LED chip is packaged in a solid plastic casing featuring two parallel pins. These DIP chips are then plugged into the sockets on the boards or soldered directly to the pad. Low-power LEDs (<0.1 W) whose current is relatively low (20–30 mA) often use DIP packaging. The typical size of the DIP package is 3-5 mm.
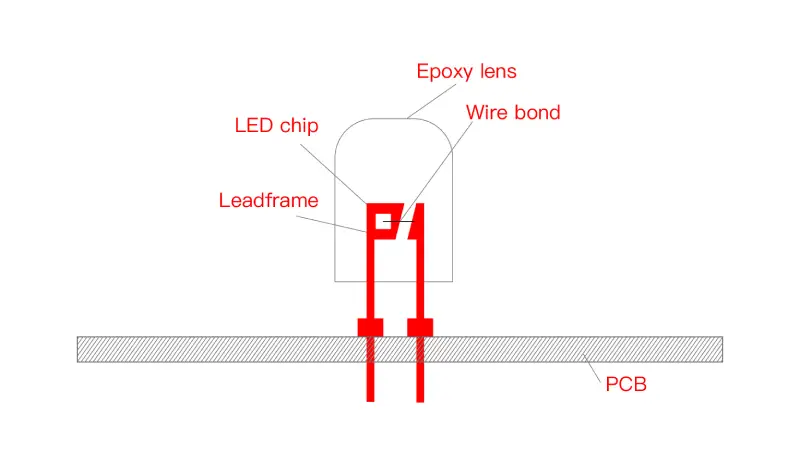
Pros of DIP packaging:
- Easy installation and maintenance: The orderly arrangement of DIP packages allows for effortless plugging and unplugging from the boards.
- Excellent compatibility: DIP packaging is the earliest form of technology that emerges on the market, so it is compatible with various devices.
- Resistant to dust and high temperatures: The plastic case is of high quality. It can protect the chip from the influence of dust, moisture, and shock, and can work in high-temperature environments.
Cons of DIP packaging:
- Fragile pins: While plugging in the pins manually or by machine, the pins are likely to bend or break.
- Unreliable: The pin is plugged into the socket, so the soldered area is small, making the soldering not firm enough.
- Taking up much space: DIP packaging is not suitable for small electronic products, because the sockets take up much space.
SMD
SMD is the abbreviation for “surface mounted devices,” and SMD LED is the most popular way of packaging on the market. The factories fix the bare chips on the brackets and connect each other with gold wires. Then they use epoxy resin to cover the chip. The solder joints are attached to the PCB via reflow soldering.
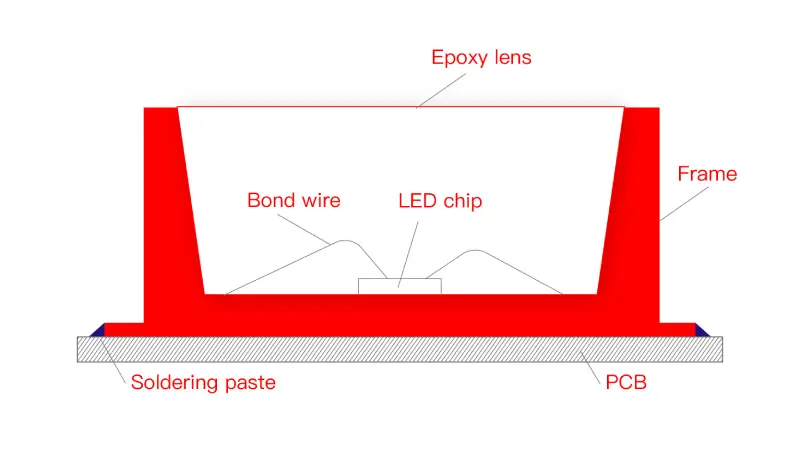
Pros of SMD packaging:
- Small size and light weight: SMD LEDs are small and lightweight, and can achieve high-density integration, which is essential to produce lightweight electronic products.
- High-frequency performance: The short pins and short connection paths of SMD package components help reduce inductance and resistance and improve high-frequency performance.
- Heat dissipation: The SMD package is in direct contact with the board, so the heat dissipation is effective. Heat dissipation is one of the most important factors of LED lighting design.
Cons of SMD packaging:
- Demanding operation environment: SMD packaging must be carried out in clean rooms, which increases production costs.
- Low production efficiency: In the process of pouring the packaging material, SMD packaging will take more time than COB packaging.
- Likely to be damaged: The pins of SMD LEDs are exposed to the air. When they come into contact with water or moisture, short circuits may occur.
COB
COB indicates “chip on board,” which means this packaging method integrates multiple LED chips and then solders them directly to the PCB (printed circuit board). This technology is usually applied to package high-power multi-chip arrays.
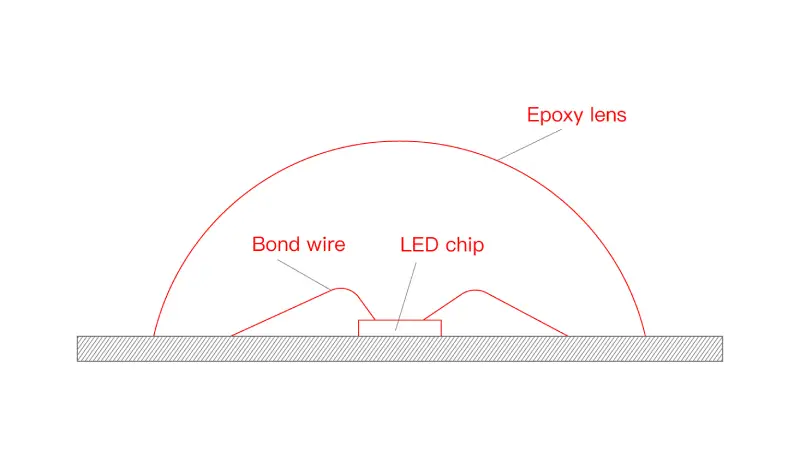
Pros of COB packaging:
- Solid: COB chips are packaged in the groove of the PCB and then fixed by epoxy resin. So if subjected to a large external force, COB LEDs are less likely to fall off.
- Heat dissipation: The heat created by LED chips can be dissipated directly through the board. It improves the power density and reduces thermal resistance.
- Smaller spacing: COB technology arranges the chips in a more compact way, making it possible for them to emit bright and concentrated light.
Cons of COB packaging:
- Demanding operation: Ensuring each chip works well is an essential step before packaging the chips. So it is not as easy as the single-chip packaging of SMD technology.
- Inconvenient maintenance: For SMD LEDs, it is common to replace each broken chip separately. However, if one chip breaks on the COB-packaged board, you need to replace the whole board.
Different power of LED chips
Size (mil) | Power (W) | Current (mA) | |
low-power chips | 5-14 | <0.1 | 20 |
medium-power chips | 20*38, 23*45, 24*24 | Around 0.5 | 20-300 |
high-power chips | 35*35, 40*40, 45*45, 50*50, 55*55 | 1-3 | 300-800 |
The specifications mentioned in the table are only common ones. The customers can customize the size as per their specific needs. Theoretically, larger chips can withstand greater current and power. Under the same standard 20 mA current, using high-power chips will not make the light brighter. They will only cost more and generate more heat.
LED chips in different colors
Color | Wavelength (k/nm) | Power (W) | Semiconductor material |
White | 6000-9000 K | 2.9-3.3 | GaN |
Warm white | 2800-3200 K | 2.9-3.3 | GaN |
Infrared | >760 | <1.9 | GaAs |
Red | 760-610 | 1.63-2.03 | AlGaAs, GaAsP |
Orange | 610-590 | 2.03-2.10 | AlGaInP |
Yellow | 590-570 | 2.10-2.18 | AlGaInP |
Green | 570-500 | 2.18-4 | GaN, GaAsP |
Blue | 500-450 | 2.48-3.7 | SiC |
Purple | 450-380 | 2.76-4 | InGaN |
Ultraviolet | <380 | 3.1-4.4 | AlN |
Applications of LED chips of different colors
- Blue: LED displays, indicators, and backlight source for LCD panels. Blue LEDs can produce white light by combining them with phosphors.
- Red/green: neon lights, indicators, vehicle lights, signal lights, and backlight sources for LCD panels. Manufacturers can produce bright and adjustable white light by combing red, green, and blue LEDs. Changing the ratio of these three colors can produce white light of different color temperatures.
- Infrared: light source of infrared remote controllers, proximity sensors, photocouplers, etc.
- Ultraviolet: sterilization and deodorization of refrigerators and home appliances, etc. Besides, it can also combine with phosphors to produce visible light.
Conclusions
Although there are various LED types on the market, by considering what color LEDs you want, where you want to use them, and the power and packaging requirements, you will be able to make the first step to choosing suitable LED types. If you want to know more about LED lights, our experts can be your guide. Talk with them right away!